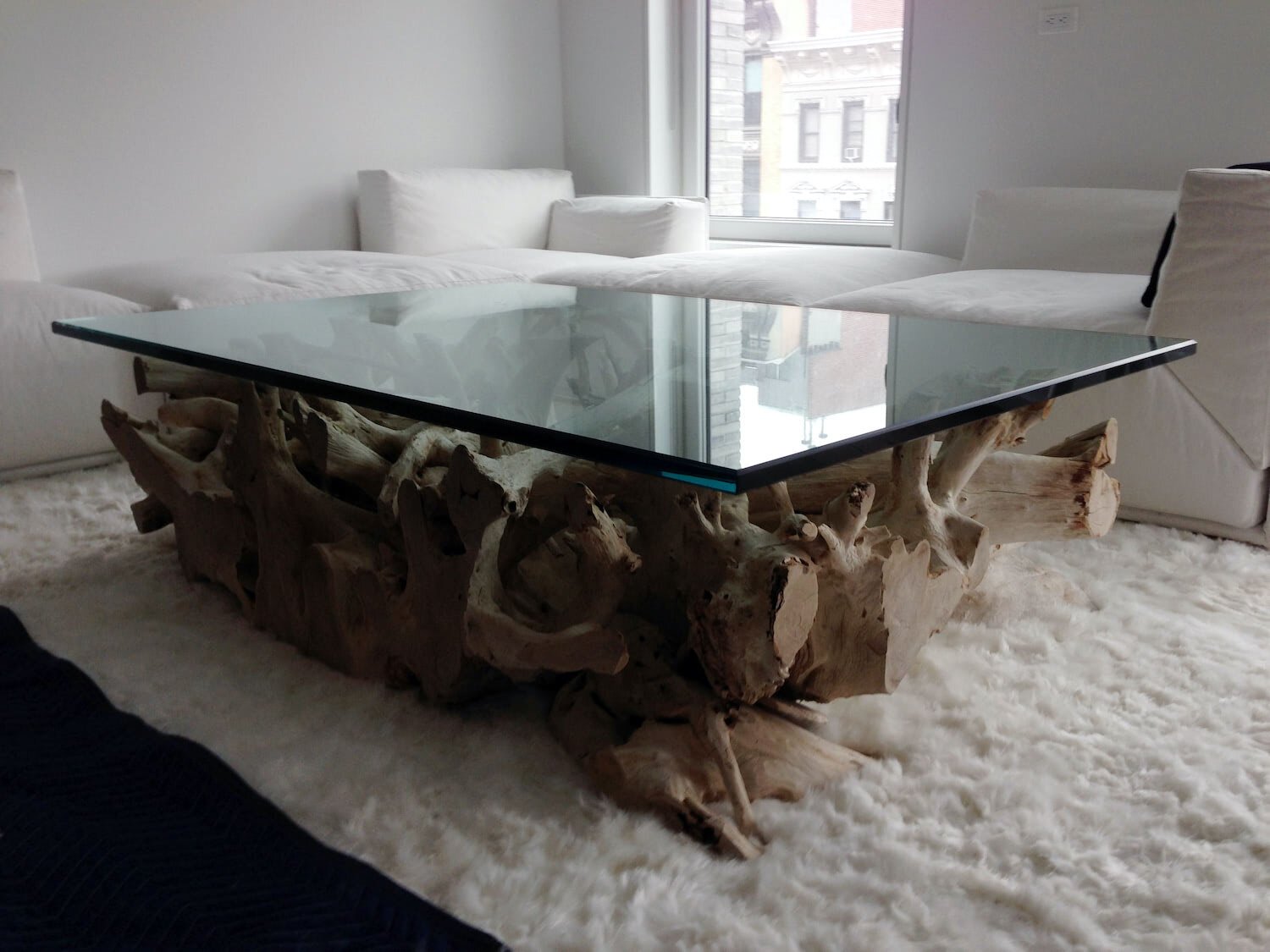
Answers to Your Questions
ColorKote was born from GlassKote, a now 25-year-old process. But even with its proven track record, there may still be questions about the process, its ability, and other important facts. Feel free to browse our FAQs below and should you have any questions that are not answered, please contact us.
-
GlassKote is the system name for our process of coating glass to achieve highly attractive colors and finishes. GlassKote was conceived in the 1950’s and commercialized some 25-years ago. During this time, literally thousands of glass panels have been coated.
-
ColorKote CT, LLC is a decorative glass fabricator and is a licensed applicator of GlassKote in the New England area and beyond.
-
Our research shows that no paint manufacturer actively promotes or for that matter recommends that its paint be used on glass. Glass is quite an unusual substrate to work with because of its chemical makeup. Normal paint applied to glass will usually peel or crack over time, and generally doesn’t stand up to humidity and other common environmental stresses.
So the answer is, that only proprietary glass coatings should be used. This way you can ensure that it will chemically bond to the glass and provide a durable and lasting finish.
-
There’s nothing more compelling than a track record. GlassKote has been installed in Australia for over 25 years and has enjoyed an excellent reputation. It is used in the most grueling environments including wet and humid areas without any trouble (take a look at the swimming pool picture in the Guarantee section). The product has been used extensively on exterior spandrel applications on buildings in Australia; a location with plenty of sun and high temperatures. GlassKote is currently sold in more than 30 countries worldwide and is backed up by a solid applicator warranty. ColorKote is proud to bring this process to the United States.
-
There are essentially three ways to color glass; by coating one surface, through adding minerals and other pigments to molten glass during manufacturing, and by laminating two or more pieces of glass with a colored material sandwiched in between. The problem with laminated technologies is that their appearance isn’t always good (the depth and quality of the color), the edges are not attractive, the material can be difficult to work, the types of glass are limited, and it can be very expensive. Coloring molten glass is often not suitable since it is translucent, there are only a handful of color options, and it’s also very expensive.
When it comes to color coatings for glass, several have come and gone, but none stand up to ColorKote. There simply has not been a product that demonstrates the durability, appearance, color range, or overall quality of ColorKote. See for yourself by asking for samples of products. You’ll quickly discover the ColorKote difference.
So the short answer is that ColorKote provides the most attractive appearance, best durability, and highest value of any glass coloring process on the market.
-
There are a number of factors that should be considered when choosing a color coating process & product:
How long has the product been in use? Can you personally visit an installation that is 10+ years old? If not, can you really trust the durability?
How does the product look in samples? Is there a real depth and richness to the color?
How does the product stand up to testing? Such testing includes scratching / adhesion, water immersion, boiling etc. Normal paint will peel and crack over time. Even automotive paint will come off of glass under humid conditions or if exposed to water. You shouldn’t be fooled by the appearance only.
Is the product safe? What type of chemicals does it contain?
What is the warranty? Will the company stand behind their work? It tells you a lot about their faith in the product?
What kind of support does the company provide? What is your pre-sales experience like? Is the company responsive? What happens if the company goes away? Can you source the product from more than one place?
-
ColorKote is a very interesting architectural material. It is easy to clean and maintain, it’s non porous, and doesn’t harbor germs or bacteria. ColorKote delivers over 10,000 exciting colors and finishes including sparkle, metallic, and granite. The inherent reflectivity of glass also provides the illusion of additional space. ColorKote outlasts most architectural finishes and provides structural strength. ColorKote has no size limitation and it can be used with virtually any type of glass including textured glass. The product is excellent for wet areas such as showers and backsplashes. Since there’s no need for grout, water doesn’t penetrate and unsightly mold and hard water stains are a thing of the past. Glass also has excellent resistance to heat when used with toughened or tempered substrate. Best of all, the product is durable and reasonably priced.
-
ColorKote supplies literally thousands of colors and finishes. Lighter colors such as pastels and off-whites are affected by the natural greenness of clear glass. As a result, ColorKote usually recommends the use of low-iron glass such as Starphire or OptiWhite, which has very little color content to the glass.
-
ColorKote adheres to virtually any type of glass including float glass, chemically strengthened glass, heat strengthened glass, tempered glass, sandblasted glass, etched glass, wired glass etc.
-
One of the key strengths to the ColorKote process is the ability to fulfill small, custom colors very easily, and the ability to exactly match existing colors. We are able to turn around custom samples for architects and designers usually in a matter of days.
-
That depends on how the glass was mounted. Most installations are done with an adhesive to firmly attach glass to a wall and cannot be removed without the glass breaking (similar to removing one large tile). However, if the glass was installed with mechanical fasteners, it can be easily changed to another piece of glass with a different color applied. But in no event can the actual ColorKote coating be removed from glass. It bonds chemically to the glass; once it is applied; it doesn’t come off.
-
ColorKote advocates the use of coating materials that are free of a chemical family known as isocyanates (commonly found in automobile coatings). Isocyanates can be quite harmful during the application phase if not handled correctly and there is debate whether isocyanates outgas after installation. We are very concerned with the environment and we consider ourselves a “green” company.
-
We have sample packages available for customers or architects & designers. We can also produce custom samples for larger projects on very short notice. Please call us for further information.
-
ColorKote CT fabricates a full range of GlassKote products. Simply call or email our office to obtain a quote.
-
Color coatings come in many varieties. Normal household paint will NOT work on glass as it will peel and crack over time, and will not stand up to water and humidity. However, companies that do coat glass generally use one of three types of coating materials combined with special chemistry to work on glass: urethanes, epoxies, and silicone based coatings.
Urethane coatings: generally considered the best overall coating. They combine durability that is close to that of epoxy with excellent UV stability, so they are suitable for outdoors use. That is why urethanes are used for automotive applications. One major consideration however is whether the urethane in question is an isocyanate-based chemistry. If so, we don’t feel it belongs in a household environment such as a shower stall or kitchen.
Epoxy coatings: very durable coatings but they have two general drawbacks. One, they are very hard and brittle. While difficult to scratch, they tend to bubble and chip of they are impacted, and usually don’t cut and edge cleanly on glass. The more important drawback is that epoxies do not stand up well to ultraviolet light outdoors. That is why these coatings are usually not recommended for outdoor applications. The epoxy resin will discolor from UV exposure – even indoors.
Silicone coatings: very stable materials, but they have a peculiar texture and appearance that many people find objectionable. Silicone can be easily scratched with your fingernail and has very poor abrasion resistance. Installation people often don’t like working with silicone materials because they are easily damaged during transport prior to installation.
-
Virtually any architectural surface can be intentionally damaged. A sharp metal instrument taken to granite, metal, wood or glass will scratch and abrade the surface. What is important is whether the surface is durable under normal use, not intentional abuse.
In the case of color coatings for glass, all coatings can be purposely scratched. However, the coating should be hard enough not to scratch under normal handling, including transportation and installation. Once installed, the coating is always BEHIND the glass and will not be abraded.
If you are testing a sample coating, you will be able to scratch it with a knife or key. What is important is how well it scratches. By this, we mean does it cut cleanly, or does it bubble and chip? Very hard coatings like epoxies will tend to chip when cut & edged on glass, because they are brittle and ultra hard. Soft coatings like silicone will scratch too easily under normal handling (you can scratch it off with a fingernail).The ideal is a durable coating with good harness, but excellent adhesion and suitable softness to undergo glass working (cutting and edging) cleanly.
So as you can see, asking “can a surface be scratched” is not a simple question.
-
Companies that apply coatings to glass sometimes publish test results for their coating material. Some of the published results are questionable because they don’t follow accepted testing standards such as ASTM (American Society for Testing & Materials) standards.
When reviewing test results, be sure to understand what you are looking at, and what it actually means in real life.
First, remember that when coating glass, the coating is BEHIND the glass and not exposed to contact. As such, many tests are not really applicable. For instance, coating flexibility doesn’t matter when applied to glass. As another example, testing for chemical resistance tells you something about the durability of the coating, but it is unlikely that you will find acids and solvents between your glass backsplash and the wall?
-
Hardness. Hardness tells you how easily a coating can be scratched and abraded. When coating glass, it is important for two reasons: First, installers may accidentally scratch the product before the glass is installed. Second, it tells you something about how the coated glass can be worked (edged & cut). A soft coating will easily scratch during transport and installation, while a very hard coating will not cut and edge cleanly. You really want a hard coating, but not TOO hard.
Adhesion. A very useful test about how well the coating adheres to glass. There are two types; cross-hatch adhesion testing and pull-off strength testing. This is a very important test since it tells you how the coating is bonding with the glass. Using plain household paint or automotive paint will yield very poor adhesion testing results.
Chemical resistance. While not that applicable once glass is installed, this test does tell you something about the durability of the coating. What is especially important is the resistance to cold water immersion and even boiling water. All coatings will soften under boiling water, but what is important is how the coating reacts when tested after boiling. Does it still adhere well? Chemicals are not likely to find their way behind an architectural piece of glass, but water may well do so.
Humidity resistance. A very important test for glass coatings. Many traditional paints will peel and crack due to humidity exposure since they don’t bond with the glass surface.
UV accelerated weathering. This test shows how the coating stands up to exposure to sun and ultraviolet rays. Coatings may discolor, or even peel or crack under UV exposure. For instance, epoxy coatings yellow under UV exposure and are generally not recommended for outdoors use. While interior applications receive less UV exposure, some ultraviolet rays still penetrate through windows.
Many ASTM tests are subjective. For instance, some types of chemical resistance tests are measured by rubbing a sample with a particular chemical, and determining how many “rubs” cause a coating defect. The results will vary between labs and even test technicians, since the pressure exerted during the rub will influence the result, as will the subjective determination of when the coating is affected. This kind of testing is most useful to compare one sample against another, but the absolute test results are not necessarily meaningful.